Strong leadership isn’t just about being tough and hard-hearted. Isn’t true leadership about driving the organization forward with determination, leading by example in solving problems, and earning the trust of team members in the face of challenges? In this edition of the Leader’s Culture Letter, we met with Roh Kyung-chul, Head of the (Pohang) Section Steel Production Group, who emphasizes that a relationship of trust with staff members is a key leadership quality.
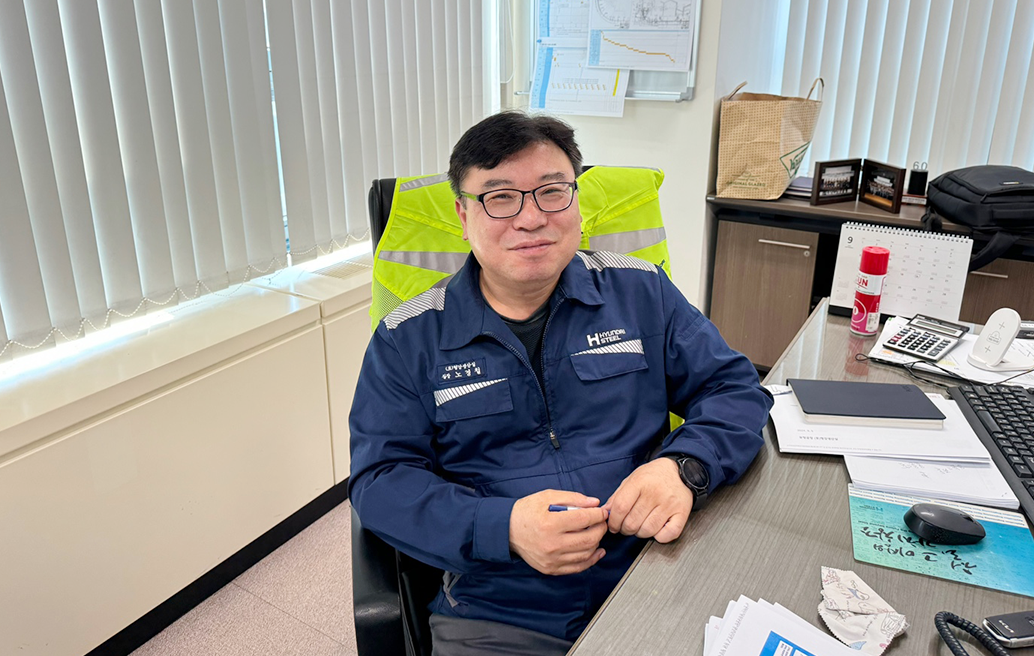
Roh Kyung-chul, Head of the (Pohang) Section Steel Production Group
Q1. What is the Section Steel Production Group responsible for? Can you introduce each team?
The Section Steel Production Group manufactures a variety of section steel products, including world-class items. The Large Scale Steel Making Team and the Middle Scale Steel Making Team produce beam blanks and billets, which serve as raw materials for our products. The Large Scale Roll Team makes H-beams, rails, sheet piles, and angle beams, while the Middle Scale Roll Team produces H-beams and section steel for shipbuilding. Finally, the Long Product Roll Design Group is responsible for the design and processing of the rolls used in the rolling process
Q2. What efforts are you making to foster a positive organizational culture?
In the Section Steel Production Group, around 45% of the workforce is G2 or lower, which means there is a high proportion of junior managers. For this reason, we place a strong emphasis on training. Since my time as a team leader, I have believed that passing on knowledge and providing training to younger colleagues is one of my key responsibilities to the company. As a result, I actively encourage job-related training and have assigned mentors to ensure ongoing training.
In addition, since my teams are split between Plants 1 and 2, it is difficult for all of us to get together. I also believe that team dinners shouldn’t feel like part of work, so I don’t hold them too often. When we do, we are pretty relaxed about them – some may start eating earlier due to different work schedules, and others join later, but no one feels awkward about it. I try to make sure everyone enjoys these gatherings by arriving early and being the first to leave. (laughs)
Recently, during a dinner with the managers, I learned that the managers from Plants 1 and 2 didn’t know each other very well. So, I’m working on creating more opportunities for my group members to interact with each other.
Q3. What is your philosophy as a leader?
My children are in college now, and when I talk with them, I often hear them say, “Dad, that’s something you should!” With this in mind, I now feel that leading by example is the most important quality. Since our group operates on-site, I emphasize that the organization only progresses when leaders, including team leaders, lead by example. There was a generation gap when I was a new employee, and there still is one now. I believe the key to overcoming this gap is setting an example through action.
I’m known at the Pohang Works for my strong character. (laughs) I’m ambitious when it comes to work, and I personally check everything to solve issues, which can make things tough for my staff as they go through trial and error. In these situations, a relationship of trust with group members is crucial. Even when I speak firmly, I believe that if I, as a leader, lead by example and build trust with them, we can come to understand each other.
Q4. What are your aspirations as a leader this year?
Our first priority is safety. As an on-site group, we have numerous individuals working together. With a larger workforce, the risk of safety accidents inevitably increases. Since I became the group head, I’ve had to spend a lot of time focusing on safety issues. I identify areas for improvement and manage them consistently, working to ensure that a culture of safety becomes ingrained in the group.
Our second priority is innovation. Being in a production group means there are many work standards and safety regulations that must be followed. While there are many fixed aspects, I believe it’s important to embrace challenges, such as introducing new technologies and equipment.
Q5. What would you like to see from your group members?
I hope group members can grow through training, finding new opportunities for the company and improving their work processes. I believe that the future of Section Steel Production Group is directly tied to the growth of the staff.
The current long products and section steel market today is facing significant challenges. While market conditions play a role, I also wonder if perhaps I, along with others, have become too complacent. Just as we addressed issues in the past through institutional and strategic efforts, I hope that we can all adapt and come together to create a breakthrough.
Q6. Which Steel Recipe do you think works best in your group?
I would choose “When problems occur, let’s focus on coming up with a solution together, rather than blaming others.
A key characteristic of the Section Steel Production Group is that when problems occur, we come together to resolve them. In production, we face more issues than one might expect, but during these times, we make a concerted effort to discuss and debate solutions, regardless of whether we are in the office or on-site.
In the steel industry, it’s impossible to overlook the importance of experience-based know-how. When my group gathers to discuss and explore solutions, many issues get smoothly resolved.
Q7. Are there any Steel Recipes you would like to expand and apply in your group?
Yes, it would be “Experiencing difficulties? A single word can change our culture.”
While communication with most on-site employees goes well, there are times when managers encounter difficulties in their work due to communication issues. Instead of highlighting differences among colleagues working on the same tasks, I hope they will try to resolve the issues through warm and open communication. To achieve this, if there are challenges in work, I would like team leaders to take the initiative to offer help.