Steel manufacturers around the world are focusing on the development of environmentally-friendly technology that can reduce pollution, such as environmentally-friendly automotive parts that can be used to move society forward. Here’s how Hyundai Steel is keeping its steelmaking business environmentally-friendly.
1. Hyundai Steel’s Eco-friendly Transformation
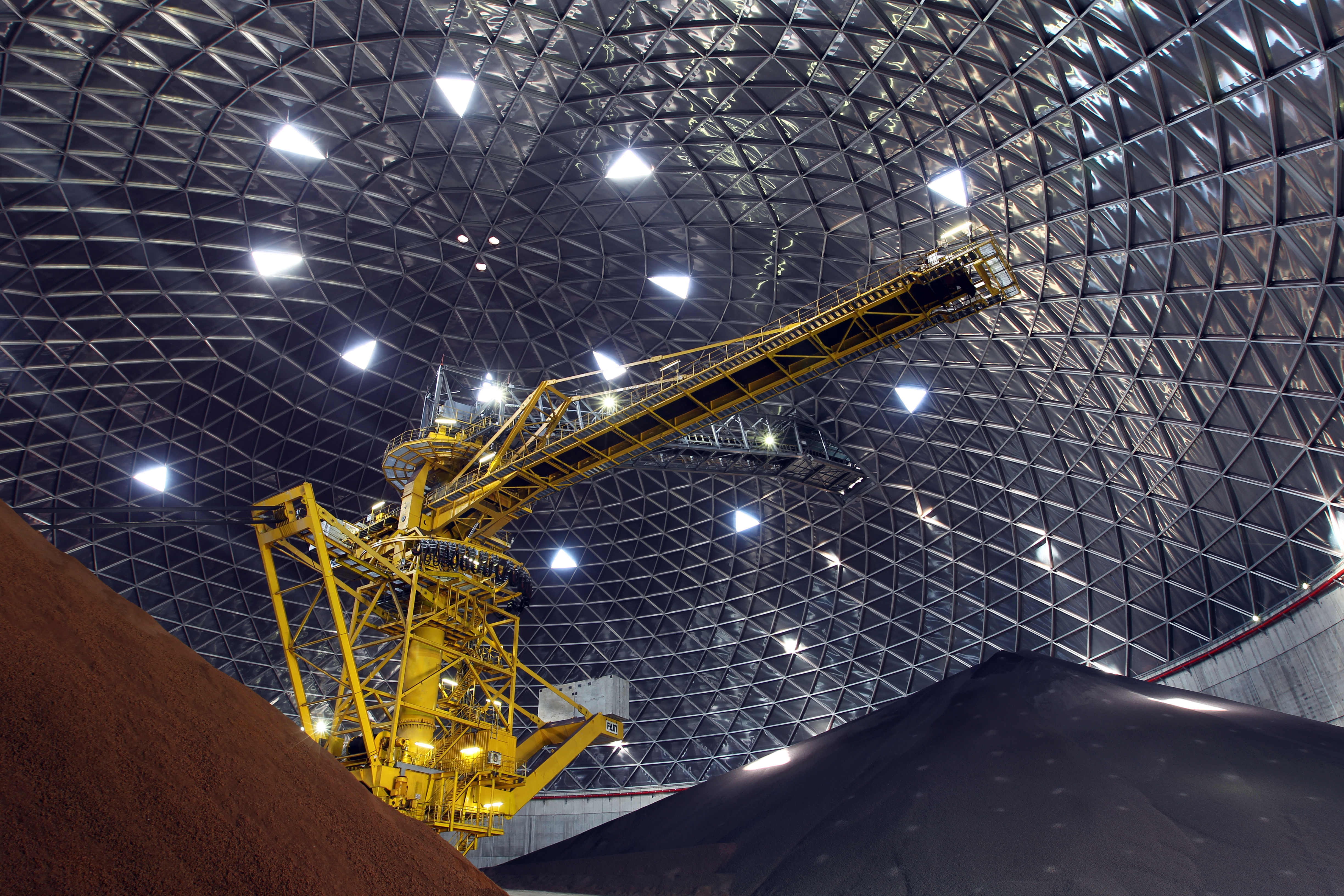
For environmentally-friendly steelmaking, Hyundai Steel adopted a “sealed material processing facility” in 2009, a move that was then unprecedented in the steel manufacturing industry. Iron ore and coal typically come in powder form and, when blown and scattered by wind, can negatively affect local environments. Hyundai Steel built its sealed material processing facility to prevent this from happening. Materials such as iron ore and soft coal transported by large ships are safely unloaded without any scattering in the air by the use of a tightly sealed continuous ship unloader and conveyor belt. The company dramatically reduced the amount of scattered dust generated from its seaside steel mills, typically exposed to strong winds, with this innovation. Since the sealed material processing facility is unaffected by weather conditions and is capable of storing larger volumes of materials compared to the open type, it also significantly reduces material management costs.
2. Special Valve for Purifying Furnace-Released Toxic Gases
A shaft furnace in a steel mill reaches temperatures of up to 2,300 °C to melt iron ore into pure melted iron. With overheating of these shaft furnaces comes a risk of explosion, which is why the “breather,” a safety valve, at the top of each shaft furnace at a steel mill, is opened three times a year. The dilemma steel manufacturers recognize is that while this exhaust is required for safety purposes,opening the valve can potentially release pollutants into the atmosphere.
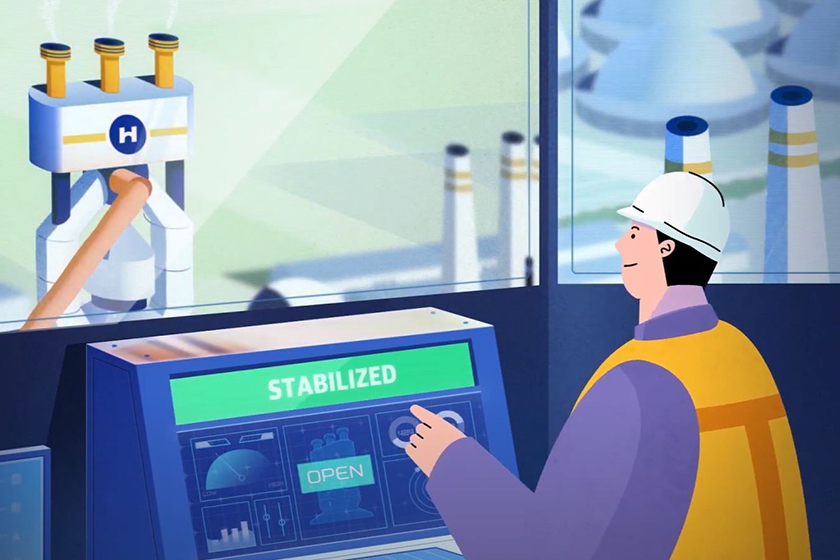
As such, Hyundai Steel, in partnership with a number of engineering technology developers around the world, has developed a “gas-purifying valve” designed to reduce pollutant discharge from shaft furnaces. Pollutants in a shaft furnace become purified through dehumidification and dust-collection facilities before finally getting discharged through the gas-purifying valve.At present, three shaft furnaces at the Dangjin Integrated Steelworks are equipped with this gas-purifying valve. Since this device has eco-friendly merit, Hyundai Steel is open to sharing the technology with interested domestic and overseas steel manufacturers.
3. Waste Water Recycling Technology and Eco-friendly Road Pavement
There are a number of other eco-friendly developments in the works at Hyundai Steel. To date, a technology that boosts the reusability of waste water-typically unsuitable for reuse due to the amount of processing needed to eliminate non-biodegradable particles and inorganic ions-to over 50% has been developed and is currently in use. “FerroPhalt,” an environmentally-friendly road pavement made from recycled steel slag, is used to pave roads on Hyundai Steel’s steel mill properties. FerroPhalt is expected to have a positive impact on the environment as it puts steel slag, once only regarded as waste matter, to good use, and can reduce the use of natural aggregate by over one million tons a year. Another ingenious development of Hyundai Steel is “FerroCon,” a concrete product made from shaft furnace slag. FerroCon is currently being used to build water pipes and manholes. Hyundai Steel is engaged in ongoing R&D to make more valuable additions to its lineup of eco-friendly products.
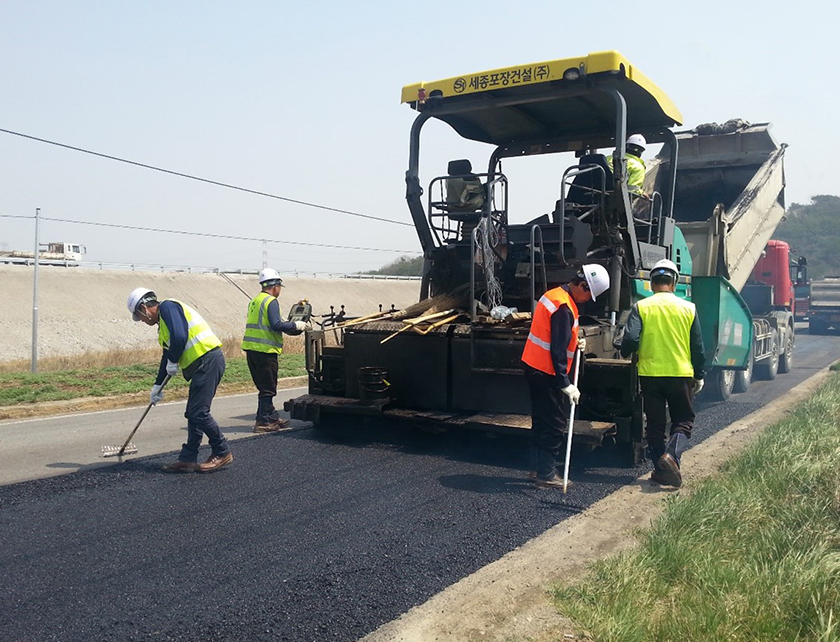