On April 27, Hyundai Steel established a material management optimization system for the 120-ton electric furnace at Incheon Works.
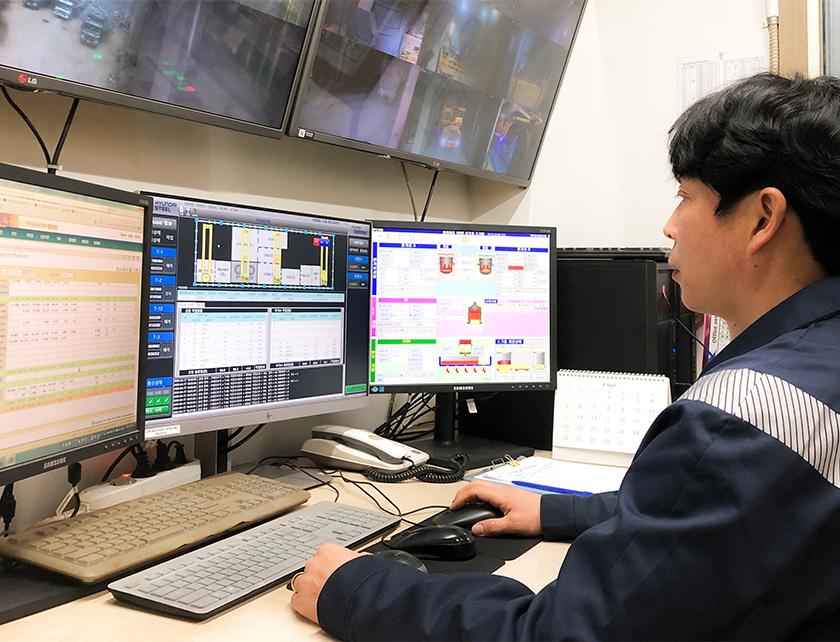
The management optimization system, designed based on big data, was previously applied to the integrated steel mill and is now being applied to the electric furnace, meaning that the smart enterprise innovation has succeeded in the steel mill industry and is now expanding into the electric furnace sector.
Under the previous material management system the mixed storage of iron scraps was unavoidable. Operators had to visibly check the iron scraps according to each order sheet and then insert them into the electric furnace. As a result, the actual grades and amounts of iron scraps used couldn’t be measured precisely, causing difficulties in product quality, operation analysis, and production cost calculation.
To solve this issue, Hyundai Steel installed a fake wall in the storage space to divide and load iron scraps by grade and created an electronic map, allowing the iron scraps to be easily identified by weights and grades, all at one glance.
Hyundai Steel accumulated and analyzed data for a period of 5 months, investing a total budget of USD 540,000. Following data analysis, a pilot system was tested, and improvements were made with regards to system operation and material usage.
A laser sensor was also installed that displays, in real time, the location of the crane managing the iron scraps. This system allows the operator to quickly and easily see the grades and locations of the iron scraps being loaded or transferred.
Another useful feature of the new system is that it automatically stores data on all the iron scraps that are transferred, stored, and used from the material storage. This information is used as raw data for quality control and operation optimization.
The accumulated data on iron scraps allows operators to predict the amount required by quality and makes meaningful operation analysis possible. This, in turn, is expected to creat a positive ripple effect for the entire production process. The new system should improve overall operation efficiency by reducing unnecessary iron scraps and predicting the expected quality of the finished products.
Hyundai Steel plans to complete even more smart enterprise innovations by 2025 by creating an optimized decision-making system. The system will be established by pursuing smart factories in the manufacturing sector and the convergence of smart management in the management sector.