A thriving organizational culture is not created by a single manager, but rather by the collective efforts of all members. To achieve this, leaders must lead by example and encourage their members to be unafraid of change. For this edition of Leader’s Culture Letter, we met with Kim Ki-jin, Head of the Plate Quality Management Group, who is not only maintaining open communication with his team in the field but also driving steady organizational change and innovation.
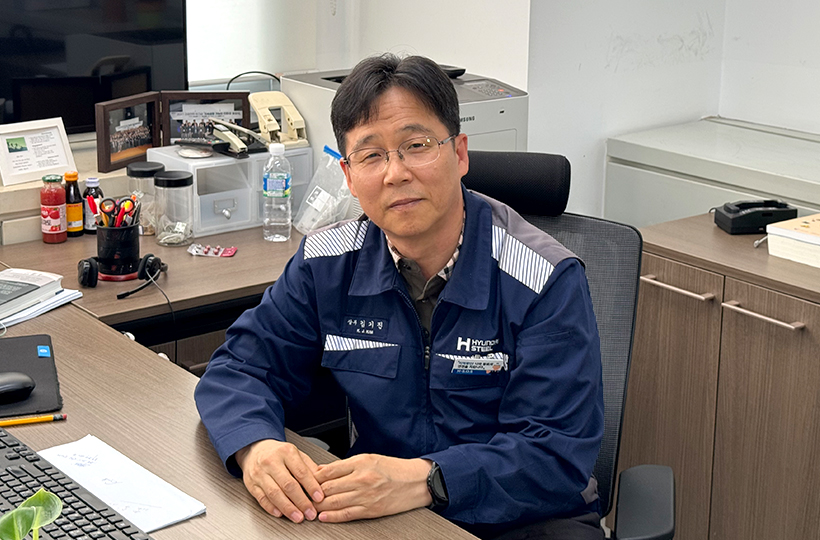
High-quality hot rolled steel produced by Hyundai Steel
Q1. As group head, what specific efforts do you make to cultivate a positive organizational culture?
I have dedicated a significant amount of time to enhancing communication with workers in the field. After spending some time at Hyundai Steel Slovakia, I returned to Korea when I was appointed the Head of the Plate Quality Management Group in 2021. On my first visit to the field, the first question I was asked was “Do we know you?” It was more about why I was there than them not knowing who I was. (Laughs)
If an organization has field operations, I believe that smooth communication with personnel in the field is more important than anything else. So, upon hearing that question, I realized I needed to put more effort into fostering communication with the field, and also with other areas. Therefore, I made a conscious effort to visit our worksites almost every day.
After about six months, we became comfortable enough to sit down together and have coffee. After a year passed, our conversations expanded beyond work to various other topics, creating a more relaxed atmosphere. I still maintain consistent communication with the teams in the field, and every week, I hold meetings with field executives to share work-related matters and benchmark each team’s best practices. In addition, I strive to enhance overall communication, not only with the field but also across different levels of the hierarchy.
Of course, even though I always keep my door wide open, and am eager to chat with my group members, they rarely come in except to give special reports. (Laughs)
Q2. What is your philosophy as a leader?
When I was preparing for this interview, I thought about the essence of leadership, and contemplated what kind of leader I am. I believe that being a leader goes beyond having a position of authority – a leader must create positive influences and foster mutual recognition to bring about the positive changes that can build a successful organization. I believe two things are needed to become such a leader.
The first is leading by example. While I was thinking about how I could contribute to my group in terms of safety, I learned that obtaining a certification would earn us bonus points in Safety Performance Indicators. So, I studied and acquired the Engineer Industrial Safety certification. During my studies, I realized that this would provide a great benefit in safety-related tasks. I encouraged our group members to obtain it, and now 37 employees from the Plate Quality Management Group have acquired the certification. Currently, some are preparing to obtain additional certifications in firefighting, chemistry, and gas to enhance their safety-related expertise. I’m also preparing to obtain the Industrial Engineer Firefighting Facilities certification (mechanical and electrical).
Second is change. People in quality tasks often lean towards being conservative because we need to deliver our products to the end customers in perfect condition. I encourage our group members not to simply replicate the methods they learned from their seniors or predecessors, but to strive to solve or address quality issues with new methods or ideas, even if they are challenging.
Q3. You have spent a long time working at overseas corporations. Did those experiences bring about any changes in your way of thinking?
During my work overseas, I spent six years in China as a production manager, overseeing everything from plant construction to production, and four years in Slovakia as a corporate head. From the perspective of leadership, which I talked about before, I realized even though the country may be different, people are fundamentally the same. I learned through experience that if I put in the effort first and lead by example, the local staff would follow suit, and we all would be striving together.
I also believe that changes in overseas corporations are happening naturally. Since the corporate heads and expatriates rotate every four years, I believe the overseas corporations are continuously evolving and developing with each new wave of leadership and change.
Q4. Is there something you would like to ask of your group members?
I would ask only that they do not simply replicate the methods they learned from their predecessors. If they only follow what they are taught, their thinking will become rigid, and they won’t explore alternative approaches, which hinders progress. I’ve talked about change and innovation many times during meetings, but the pace of change is not as fast as I would like.
However, working patterns are gradually changing, and an atmosphere is forming in which people feel comfortable about sharing their thoughts. In addition, while it is partly due to my requests, I’m also seeing a more variety of reports. Although the changes are not happening quickly, I believe we are evolving slowly but surely.
Also, I would like to add that our group is actively working to contribute to cost savings through internal innovation initiatives. I would like our group members to share these innovative activities with other groups, motivating them and fostering a sense of pride in contributing to the company’s success.
Q5. In regard to the Steel Recipe, which element is working out the best in your group?
Actually, to make an objective assessment, we held a vote on the recipe among our group members just before this interview. The recipe we selected was “Be flexible with work, but get the job done well.”
It seems that this outcome may be attributed to the effective implementation of policies such as flexible or remote work. It appears that both team leaders and members are organically making good use of the company’s policies.
Q6. Finally, are there any recipes you would like to expand and implement?
Even though “Endlessly tweaking the format of the report won’t change its substance” got the most votes from group members, I would like to apply the recipe “Past methods are only for reference. New approaches are the beginning of change” in our group, as this reflects the spirit I mentioned earlier regarding change.
But when I reflect further on the two recipes, they seem to convey a similar message. I believe our group members chose this recipe because they often report or create reports using the same old formats, without exploring new ideas or methods. If all of us in the group, including myself, use past practices only as a reference and build upon them with new frameworks and insights to proceed in the best way possible, I believe that we can evolve more as an organization.