Hyundai Steel, together with the Hyundai Kia Namyang R&D Center for Basic Materials, has successfully developed and begun mass production of a 1.8 GPa premium hot stamping steel sheet.
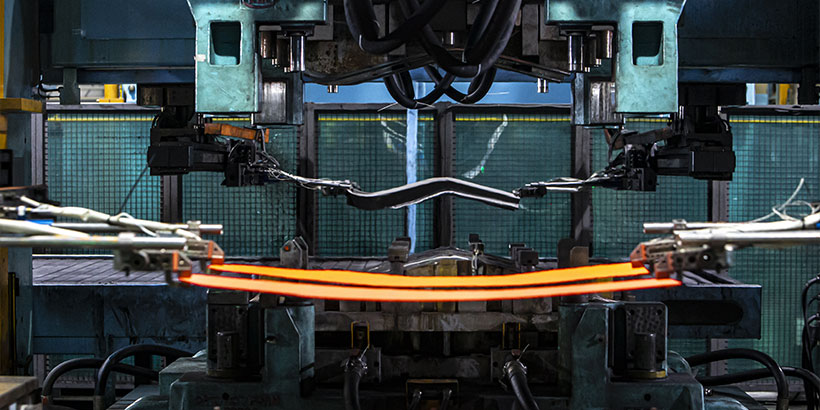
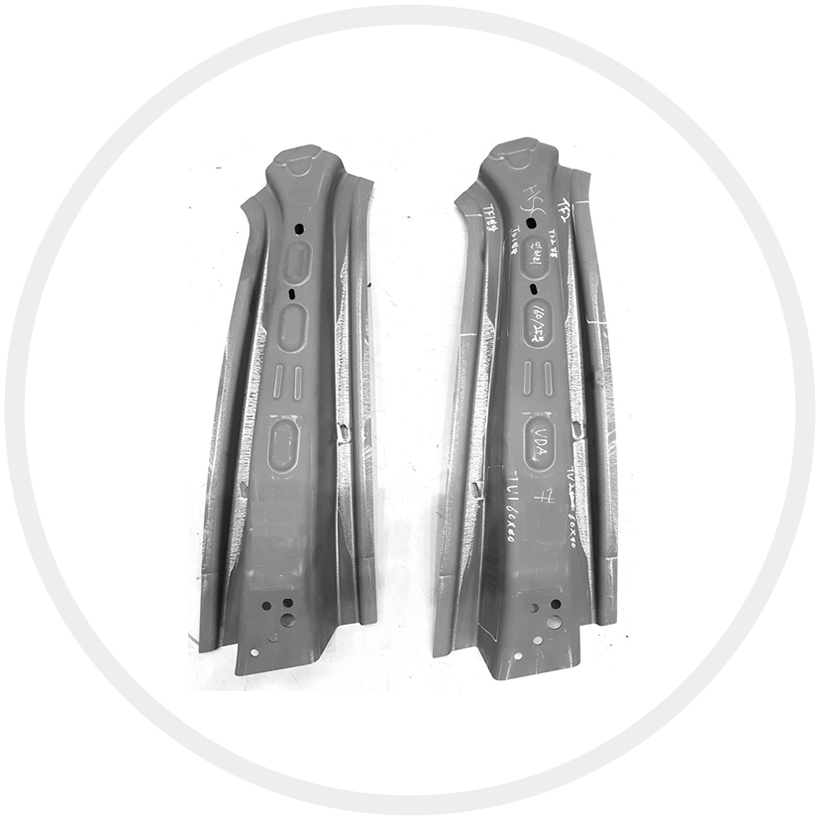
According to Hyundai Steel, the new steel grade is being provided for the production of the next-generation electric vehicle Genesis Electrified G80 (G80 EV) and the new G90. Supply of the steel sheet to Hyundai Motors began last year and starting from this year, a total of 145,000 sheets will be produced every year. This amount of steel sheets is enough to produce about 30,000 electric vehicles.
The 1.8 GPa high-strength, hot stamping steel not only helps reduce the weight of the finished vehicle but also increases passenger security. The new steel has a 20% higher tensile strength and a 10% lower weight than the original 1.5 GPa hot stamping steel.
For the production of the original hot stamping steel, the steel plate is heated to over 900℃ in a heating furnace, and then is quickly cooled in a mold. In order to develop the new steel, Hyundai Steel and the Hyundai Kia Namyang R&D Center broke away from the conventional production method and developed a specialized construction method in which the temperature of the heating furnace was reduced by more than 50℃.
The new production method also prevents hydrogen components from infiltrating the steel plate, helping prevent cracking within the plate. Due to these improvements, the newly developed steel plate is stronger than other types of plates and has better weldability. The new production method, through a reduction of the temperature of the heating furnace, saves energy for increased eco-friendliness while also improving the quality of the finished steel plate.
Hyundai Steel has built hot stamping production lines in Yesan-gun in Chungcheong-do Province and in the Ulsan region (both located in South Korea) in order to secure a strong foothold in the eco-friendly automobile construction material market. The company is also continuing to make other investments designed to improve its competitive edge in the global market. In November 2020, the hot stamping production plant in Ostrava, Czech Republic built a production line for high-strength automobile components that produces 3.4 million steel sheets (enough to build 200,000 vehicles), which are supplied to Hyundai Motors’ Czech plant.
The demand for high-strength, lightweight materials for the production of eco-friendly vehicles continues to significantly increase. Since eco-friendly vehicles are inherently heavier than conventional vehicles due to the weight of the battery and increased electric parts, reducing the overall weight of an electrical vehicle to secure mileage is becoming a top priority for car manufacturers.
The Hyundai Motor Group is gradually increasing its application of hot stamping components to reduce the weight of its eco-friendly vehicles. About 15% of the hot stamping steel produced is actually applied to internal combustion engine vehicles, while its use has been increased up to 20% for electric vehicles.
Hyundai Steel is not only using hot stamping to reduce vehicle weight but is also integrating various component production processes. Currently, 1.8 GPa hot stamping and Tailored Welded Blank (TWB, a material that reduces weight by incorporating tailored welded blank technology) are being developed by the Hyundai Kia Namyang R&D Center.
The “TWB hot stamping 1 GPa material for vehicles” is a prime example of the joint developments being made by Hyundai Steel and the Hyundai Kia Namyang R&D Center. This new material is now being used as a center filler component that reduces the weight of the center filler by about 10%.
Also, Hyundai Steel plans to increasingly use advanced technologies to affect changes in the industry and create a “green factory” by developing steel for vehicle production—such as ultra-high tensile strength steel with high formability and highly tough hot stamping steel—and increase overall production efficiency by recycling byproducts and maximizing the production process capacity.