According to a survey conducted by IBM, people create approximately 2,500 quadrillion bytes of data each day, and this number increases approximately two-fold every 18–24 months. As such, it’s no surprise that data analysis is becoming increasingly important for companies to be able to effectively operate their budget and identify areas requiring further investments.
Big Data with Operating Expertise
Hyundai Steel utilizes big data to improve its system for predicting and controlling the quality of its hot-rolled steel. In order to prevent collisions between different slabs of steel, which occur when the slabs are curled up like coils prior to being flattened as part of the rolling process, the company has introduced the “Mill Pacing Control (MPC)” program, applied to hot-rolled steel plates manufactured in various sizes. The MPC program applies big data to work processes, marking a shift away from manual entries by human operators. Through the use of big data, Hyundai Steel is now able to predict the manufacturing time and final quality of its steel plates, and the accuracy rate for predicting coil width has increased by over 98%. Machine learning, a function of the applied processes, has also led to an annual production increase of 150,000 tons at Hyundai Steel’s 2nd rolling factory.
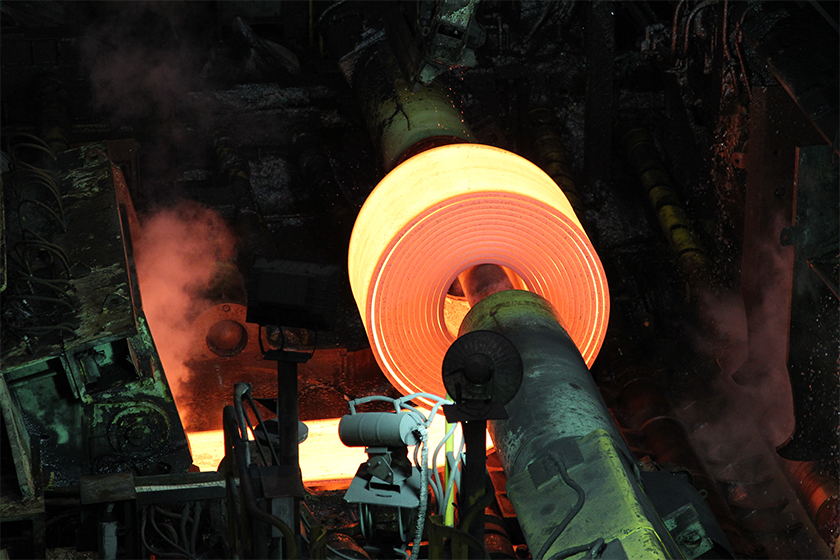
Accurate Steel Scrap Management Using Big Data
Hyundai Steel utilizes big data for the management of its steel scraps, which are an important ingredient for the company’s steel products. Prior to the use of big data, human operators had to visually assess the steel scraps according to order sheets and then insert the scraps into the electric furnace. This resulted in partial mixes of ingredients of different grades. The manual system was replaced with a big data-based system and infrastructure that automatically enters all the information on the steel scraps transported, stored, and inserted through the raw material warehouse, decreasing the inefficient use of steel scraps and enabling the accurate prediction of future product quality. Hyundai Steel is reviewing the application of the big data system to the electric furnaces at all of its plants, starting with Incheon Works. Once the systems are all implemented, the company expects to see budget savings of more than USD 6 million.
Training Big Data Experts
In August 2019, Hyundai Steel established a dedicated Smart Factory Team at Dangjin Integrated Steelworks and is currently operating a training academy. The Smart Factory Academy is a basic training course that cultivates workers who are trained for and dedicated to smart factory operations. The first training session yielded a total of 47 graduates. Some of the graduates are now taking customized training courses at outside companies specializing in related fields and are carrying out three test assignments to improve the company’s smart operation processes and to advance their own big data skills.
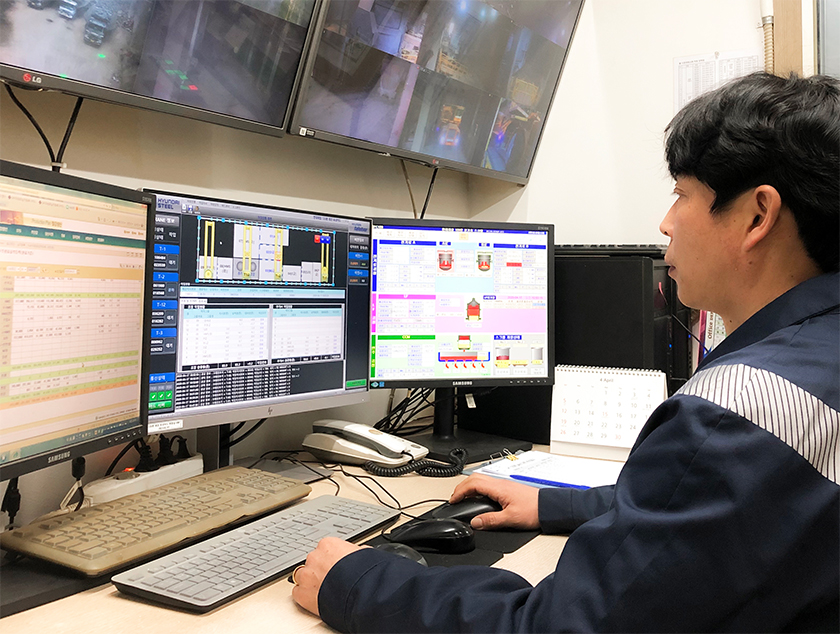